When you want to produce NPK fertilizer, there are two granulation method for your choice. They are granulation method and dry granulation method. You can use them to make powdery or granular NPK fertilizer. And SX, as a professional fertilizer equipment manufacturer, can provide you with some various proportion of NPK compound fertilizer production lines. If you are interested in it, please contact us immediately.
More NPK Fertilizer Making Solutions for your Choice
Except for the above two npk fertilizer production line, there are some other npk fertilizer making plans with our past customers. Whether you want to make bulk blending or compound fertilizer, powder or granule, 17:17:17 or 20:10:10, they can fully meet your requirements. In addition, we can design fetilizer plant according to your actual conditions. Come to get your own fertlizer production project!
NPK Fertilizer Plant Cost
Cost plays an important role in NPK fertilizer plant setup. But it is not fixed and will change with capacity, design, equipment type, etc. Here are some information about NPK fertilizer plant cost for your reference. Including NPK compound fertilizer plant cost and NPK fertilizer granulator cost. As a reliable and leading fertilizer equipment manufacturer, SX will provide you with a favourable price. If you have any requirements or get precise quote for your NPK fertilizer making machines, welcome to contact us immediately.
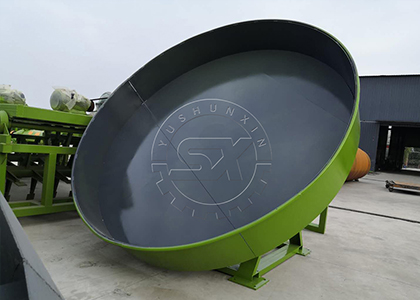
NPK Granulator Cost
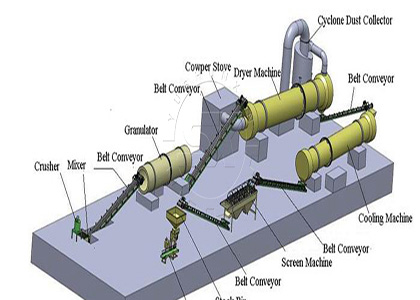
NPK Fertilizer Manufacturing Line Cost
What Proportion of NPK Fertilizer Plant can SX Provide for you ?
SX can provide you with various proportions NPK fertilizer plant. Powdery and granular NPK fertilizer plant are for your choice. What’s more, if you want to customize the this production line, we can also meet your requirement according to your conditions. So what is the design of NPK fertilizer production line?
17:17:17 Powder NPK Fertilizer Plant
Dynamic Batching Machine
You may want to produce 17:17:17 NPK fertilizer, how to make the proportion of N, P, K is in line with your formula? Our dynamic batching machine equips each material hopper with an electronic belt scale. In this way, it can feed materials precisely to make required NPK fertilizer. What’s more, the batching bin is equipped with a stirring device to improve production efficiency.
Chemical Material Crusher
The finer chemical powder, the better the final NPK fertilizer quality. Therefore, a suitable crusher is necessary for your NPK compound fertilizer making.Here, vertical type crusher and cage crusher are both excellent choices for you.
Powder Screening Machine
Can we package 17:17:17 NPK fertilizer powder directly after crushing? No, fertilizer crushing is not the end. In order to prepare better NPK powder, you need to add a powder screener after chemical material crusher. Rotary screening equipment will further remove waste from fine NPK powder.
Automatic Bagging Machine
Finally, you can pack 17:17:17 powdery fertilizer with automatic bagging machine. According to your capacity, we can offer you single/double buckets fertilizer bagging machines and ton fertilizer packaging scale.
20:10:10 NPK fertilizer Granulation Plant
If you plan to prepare 20:10:10 NPK fertilizer which can help you make more profits, our NPK fertilizer granulation line is an ideal choice for you. It can help you make powder chemical materials into NPK fertilizer granules quickly and easily. Then what is the design of NPK fertilizer granulation line? (Tips: The previous steps are the same as the production of powdery NPK fertilizer, and it is different from the beginning after sieving.)
What Granulation Process You Can Choose to Make NPK Fertilizer?
Most npk fertilizers are granular, but the manufacturing process is indeed different. There are two granulation process for your choice. Dry granulation and wet granulation. You can choose them according to your requirements.
NPK Fertilizer Processing Line Setup Project
When you want to setup a npk fertilizer production line, there are some factors for your reference. Such as, factory area, npk fertilizer making machine and npk fertilizer manufacturing processing. Welcome to contact us!
NPK Fertilizer Production Line Boost your Fertilizer Business
Thanks to its good sales,NPK fertilizer is one of leaders dominating the fertilizer market. With the rapid development of agriculture in most countries recently, the demand for NPK fertilizer have skyrocketed, bringing an allure to many businessmen who once had an idea of making money in the fertilizer industry. For most investors, an NPK fertilizer factory is seen as a cash cow for its ability to produce . a large amount of fertilizer which can be sold at a good price.
Thus, it is a perfect time to start your NPK fertilizer business now! Before you act, a NPK fertilizer production plant equipped with high-quality equipment is what you need first. As a professional NPK machinery manufacturer, we will provide you with a whole set of NPK production line and guide you to erect a commercial NPK fertilizer plant with ow investment. Thus,you can make economic benefits from your NPK business set up with a small amount of capital.
Npk fertilizer production line layout
Customers generally have a lot of concerns about the choice of equipment. Our company will provide very reasonable pre-sales services to help customers plan and layout the fertilizer production site. So that the cost can be saved to the greatest extent.Our company will assign engineers to visit the site and give design drawings.
Plan the placement of equipment according to the size of your site, such as fertilizer crushers, granulators and packaging machines are small in size, so you can adjust the position at any time according to other equipment during planning. Larger equipment such as manure dryers and coolers should be placed after planning to avoid repeated movement.
How many areas does a npk fertilizer production line cover?
In the world of fertilizer production, understanding the spatial requirements of an NPK fertilizer production line is crucial for planning and optimizing your manufacturing operations. Whether you’re considering a powder or granular NPK production line, the area it occupies directly influences your factory layout, operational flow, and overall production efficiency. Below, we delve into the specifics of the space requirements for both powder and granular NPK fertilizer production lines.
In conclusion, when considering the establishment of an NPK fertilizer production line, taking into account the space requirements is essential. Whether you opt for a powder or granular line, the space your line occupies impacts not only the initial setup but also the long-term operational efficiency. By adequately planning for these spatial needs, you position your fertilizer production operation for success, ensuring you have the capacity to meet production demands in an effective and efficient manner.
How to dispose of dust in your npk fertilizer manufacturing line?
In your NPK fertilizer manufacturing line, it’s essential to manage dust effectively to meet environmental regulations and protect worker health and working environment. There are two ways for your choice. Dust collector and dust cover.
Dust collector
We design a dust collection system specifically for the type of dust produced. And cyclone dust collector, bag filter dust collector, or water curtain dust collector are commonly used to capture airborne particles. In addition, you can not only install dust removal equipment in the drying and cooling process, but also in the early batching process. Because during the batching process, load type feeder feeding will also cause the generation of dust.
Dust cover
In addition to dust collector, you can also install dust covers on equipment that easily generates dust. Such as npk fertilizer granulator, screening machine, belt conveyor, etc. And we have customization services to design dust covers according to the characteristics of different equipment. So you don’t worry about them not fitting the device.
The dust collector system should be adequate to ensure the dust level ( SPM = suspended particulate matter) inside the npk fertilizer plant should be less than 50 mg/m³. So all these designs can meet your standard suspending dust less than 50mg/m³.